Hot and cold metal forming processes
As production rates accelerate, the aerospace industry is constantly seeking to improve the quality of parts and to reduce costs, particularly through the introduction of innovative processes. This is particularly the case with air inlet lips made of aluminium alloy, which have stringent specifications in terms of mechanical and aerodynamic performance, but also in terms of aesthetic appearance.
The project concerns the development of innovative processes for hot and cold forming of an aluminium alloy to create a lip section (leading edge of an engine air inlet). It focuses in particular on the development of a mixed HF/SPF (Hot Forming/Super Plastic Forming) process and cold drawing.
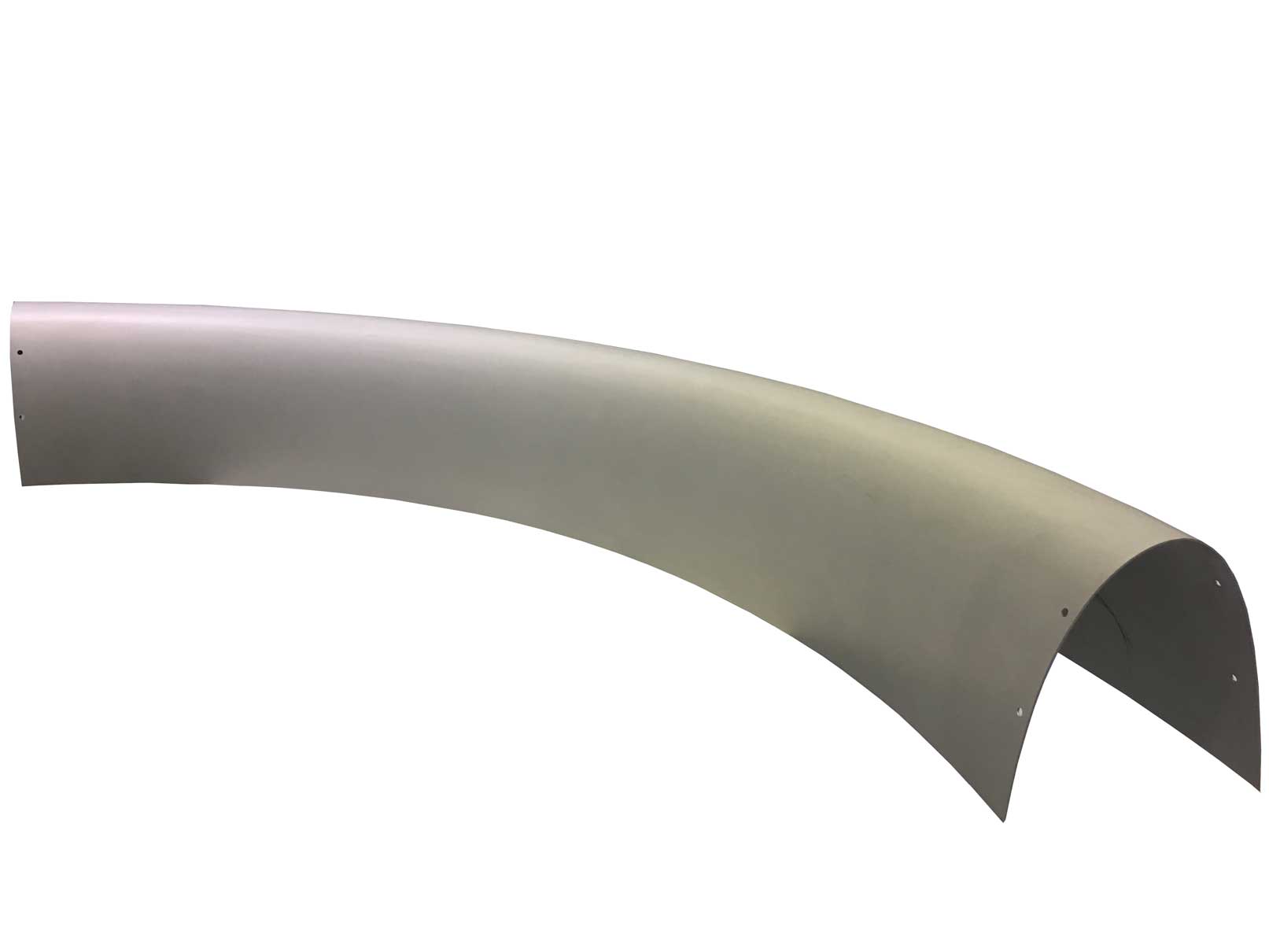
Industrial Impacts
- Improved productivity
- Improved control over quality of parts
- Reduced manufacturing costs
Expertise
- Robotics & Cobotics
- Modelling & simulation
- Composite processes
- Metal processes and additive manufacturing
Partners
- IRT Jules Verne
- ACB
- AIRBUS
- ARTS ET MÉTIERS ANGERS